Science in the Raw
3-D printing of skin starts at the scrap yard for Binghamton University researcher
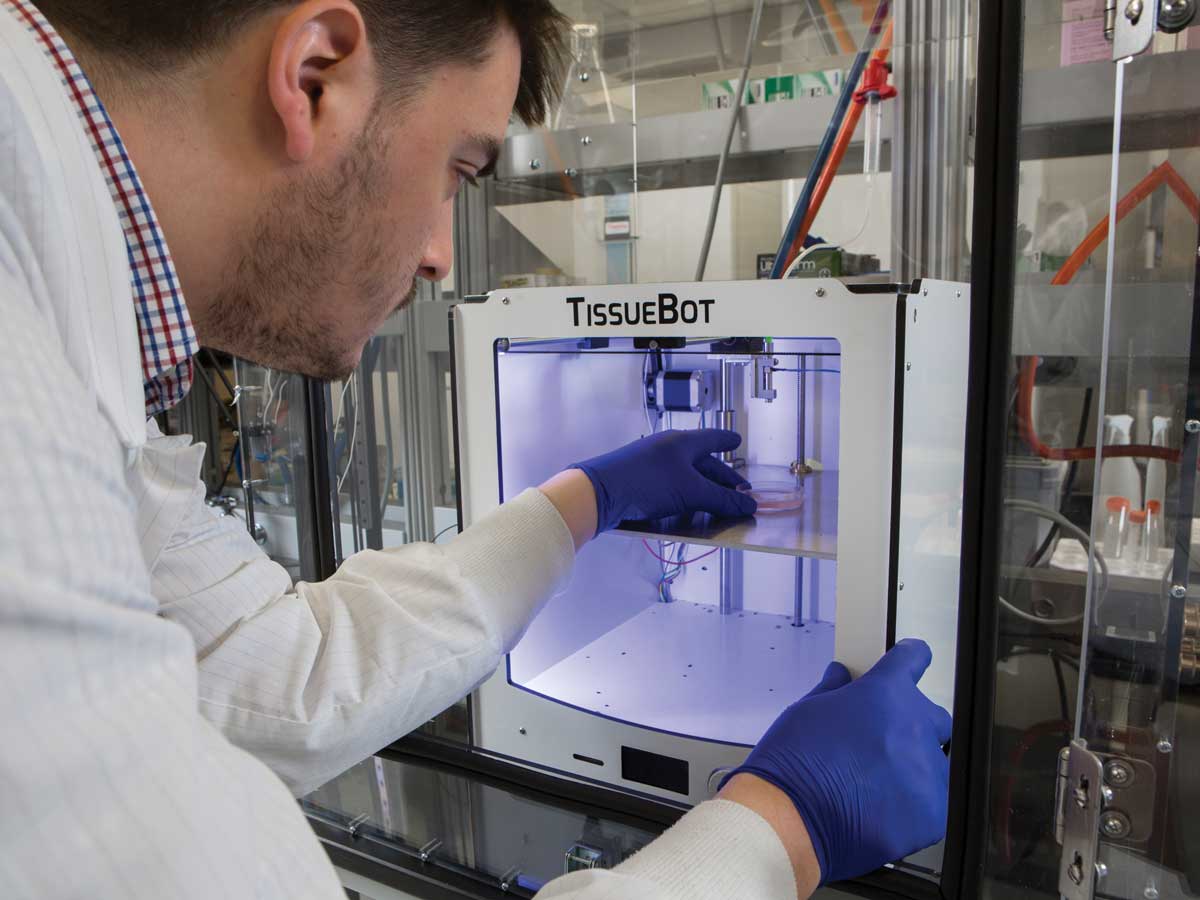
In a video titled “Printing the Future,” Binghamton University doctoral student Kyle Reeser, MS ’14, explains his research into the 3-D printing of human skin. The biomedical engineer looks at home in his white lab coat among the sophisticated equipment.
What the video doesn’t show is Reeser, with white hard hat and grimy hands, pulling sheets of raw aluminum from a bin at Pacemaker Steel & Piping in Johnson City, looking for the pieces he needs to create a new “build plate” for his 3-D bioprinter, which he has christened the TissueBot.
Reeser, 26, studied biochemistry and physics at SUNY Fredonia before coming to Binghamton for his master’s and doctoral degrees. He built the TissueBot in three months, and he and fellow doctoral student Sebastian Freeman continue to make adjustments to advance the technology.
That means seeking wisdom and materials outside of the lab.
The parts he can’t find at the local hardware store are sought from places like Japan, Switzerland, Pacemaker or the scrap pile in the University machine shop. He learns as he builds.
“The majority of my education was mostly theoretical,” Reeser says. “I took a course in circuit analysis, but I never soldered my own circuit.”
“Many times, students may be strong in biology, but not very strong in devices, so when they have an experiment, they have to either rely on somebody else or they have to buy the equipment,” says Kaiming Ye, chairman of the Department of Biomedical Engineering and Reeser’s advisor. “In his case, he is always thinking, trying to make the device by himself.”
The TissueBot is about the size of a small ottoman. It houses a gantry for interchangeable modules, created by Reeser, that can sterilize using ultraviolet irradiation, dispense cells, extrude gels and nebulize chemicals over the prints.
“A lot of labs are doing this stuff by hand, so they’ll use a 3-D printer to deposit droplets of the liquid, but then they’ll have to physically go in with a humidifier in the machine and spray [the prints] down,” Reeser says. “The cells are not happy when they are not at 37 degrees with 5 percent carbon dioxide and 100 percent humidity.”
Bioprinters have a long way to go before they can print a pancreas or a heart. They are exorbitantly expensive and are limited to specific uses, Reeser says. He hopes to make the TissueBot versatile enough and financially viable for use in laboratories around the world.
“If you have to pay $85,000 to get something that is less powerful than my machine before you can do any 3-D printing, then 3-D printing is never going to go anywhere,” Reeser says.
Testing his mettle
The sheet of aluminum from Pacemaker will next be taken to a machine shop to be cut and shaped into a new build plate with the ability to align and secure “well plates,” or tissue-culture dishes.
Reeser first has to draw up diagrams, create a computer-aided-design model and consult with technicians. Over the course of his graduate studies, he has had to teach himself how to write in several computer-programming languages, how to design and produce circuits, how to solder and cut, and how to culture cells.
“I think that being a PhD student in biomedical engineering is just about the best place that you can be,” Reeser says. “It fascinates me how many hats I get to wear throughout the week.
“Making sure I understand, exactly, every aspect of the machines I build is extremely important to me, and the only way you can do that is to talk to those more knowledgeable than yourself.”
“All of that all at once?” asks Robert Pulz, the mechanical technician at the University machine shop, after Reeser explains his design for the build plate. A series of rectangles and circles embedded in the center of the board looks like a complex symbol of the future. Pulz looks at it and notes drily, “It would be a huge pain.”
Still, Pulz appreciates Reeser’s efforts to draw diagrams of what he needs. “It might not be straight and it might not be pretty, but he knows what he needs to make it work,” he says.
It takes Pulz about eight hours to cut and polish the build plate. The next step is to drill holes into it. The plate will not screw into the machine if he does not line it up properly. “Now we’ve got to hope and pray,” Reeser says when Pulz finishes. It’s a relief to both when it installs perfectly.
The “bio” part of 3–D printing
Aside from learning bioprinting technology and building the machine, Reeser also researches how best to incorporate vasculature into 3-D printed tissue and the pigmentation of printed skin.
“You build the machine, and then the work begins,” he says.
In the lab, Reeser makes material that is printable and will sustain living cells. “We have a large bag of frozen rat tails in the freezer,” he says. They are used to make collagen, which can be used to print a scaffold on which cells will attach.
Collagen and other bioprintable materials, unlike plastic, are often difficult to build up in three dimensions. It’s not unlike working with Jell-O, Reeser says, because the structure can topple after a millimeter if each printed layer is not allowed to gel to provide support for the next layer.
Other raw materials come from a slaughterhouse in Cortland, N.Y., which will coordinate a pig slaughter with a visit by Reeser and other grad students. Some of the students need the heart or the pancreas. Reeser takes the blood vessels, packing them in ice for the trip back to the lab.
Reeser admits it’s a lot of work. But he is optimistic about the future of bioprinting.
“The more you learn about something, the more accessible it becomes,” he says. “Building a machine to build something in three dimensions is not hard. And that surprised me, because it sounds hard. Producing the technology is an engineering challenge, but the implications of the technology are boundless.”