Scott Schiffres earns NSF CAREER Award
Mechanical engineer looks for alloys to dissipate heat more quickly than materials in current use
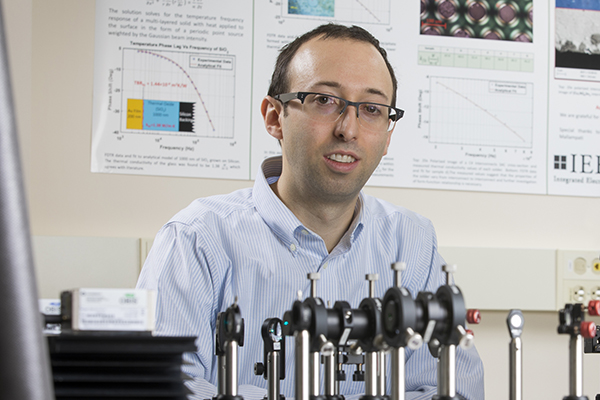
Anyone who has had a computer or cellphone overheat will appreciate the research that Scott Schiffres, assistant professor of mechanical engineering, is conducting with support from a five-year, $500,000 National Science Foundation CAREER Award.
His project, which will be fully underway in the fall, is titled “Intermetallic Interfacial Thermal Transport for Advanced Electronics Manufacturing,” and his goal is to find new alloys that form intermetallics – metal alloys with defined crystal structures – onto silicon with thermal properties that can dissipate heat more quickly than materials in current use.
The work has important applications to additive manufacturing – the process of joining materials to make objects from 3D model data, usually a layer at a time – as well as electronics packaging and superalloys (high-performing alloys), yet has been relatively unstudied from a thermal perspective. “This could help with microprocessors and power electronics such as cell phones, optical devices like lasers and power amplifiers,” Schiffres said. “Electronic components, primarily.”
“When two materials meet, there’s a bottleneck due to the surface roughness and the connection with other materials,” Schiffres said. “The purpose of the project is to look at this interfacial resistance and develop intermetallics that can fuse and grow onto silicon or other substrates and then compare the thermal conductance through these intermetallics versus those that are just metal alloys.”
One idea Schiffres is working on involves printing heat sinks directly onto chips.
“A heat sink is a structure that has high-surface-area “fins” that basically increase the area over which air or liquid can cool the chip, so heat dissipates more rapidly,” he said.
Schiffres and his research team of PhD and master’s students utilize a selective laser melting metal printer on campus, which he said is not common in academia. The NSF CAREER Award allows him to support his graduate students and cover the expenses of using the metal printer. “This infrastructure is critical and gives us the freedom to test whatever alloys we want,” he said. “Having the ability to develop our own materials is really crucial to our work.
“When we print heat sinks with the laser, the metal bonds and forms an intermetallic on the surface. If it was a heat sink made the conventional way, it wouldn’t form an intermetallic, which is very hard and should have better conduction of heat with the electronic substrates than a random alloy,” Schiffres explained.
A number of different intermetallic and silicide materials will be created for the project, Schiffres said, naming titanium silicide, tantalum silicide, zirconium silicide, and a few others as a start. “The idea is to make a silicide (silicon plus a metal that forms a crystal) with different metals and see how the conductance compares.””
There’s also an educational component to Schiffres’s project, and for this, he involves undergraduate students. “We’re integrating outreach with K-12 schools and for that we’re designing a program that teaches all three modes of heat transfer for additive manufacturing – conduction, convection and radiation – all in this one outreach activity.“
“We’re also running a design competition now for heat sinks to teach graduate students in my additive manufacturing class about the heat transfer applications of additive manufacturing,” he said. Printing of the heat sinks has begun, and will likely take a few days depending on how many layers, each about the width of a human hair, are required for each design.
Once the printing is complete, students will measure the thermal resistance of the heat sink to determine which design keeps chips the coolest. Schiffres never really thought about intermetallics before joining the faculty at Binghamton, he said, but they are “a big part of the electronics packaging research center here,” so he turned his attention to the idea of printing the heat sinks and striving for better cooling methods.
“If we can keep the chips only seven degrees cooler, that will double the time to failure and reduce power consumption,” Schiffres said. “Manufacturers could then choose to run a device at a higher power, or extend its life and conserve energy.”