COVID-19: Watson School teams make progress to aid coronavirus fight
Healthcare partners testing prototypes of ventilator adapters, masks, face shields and UV sterilizer
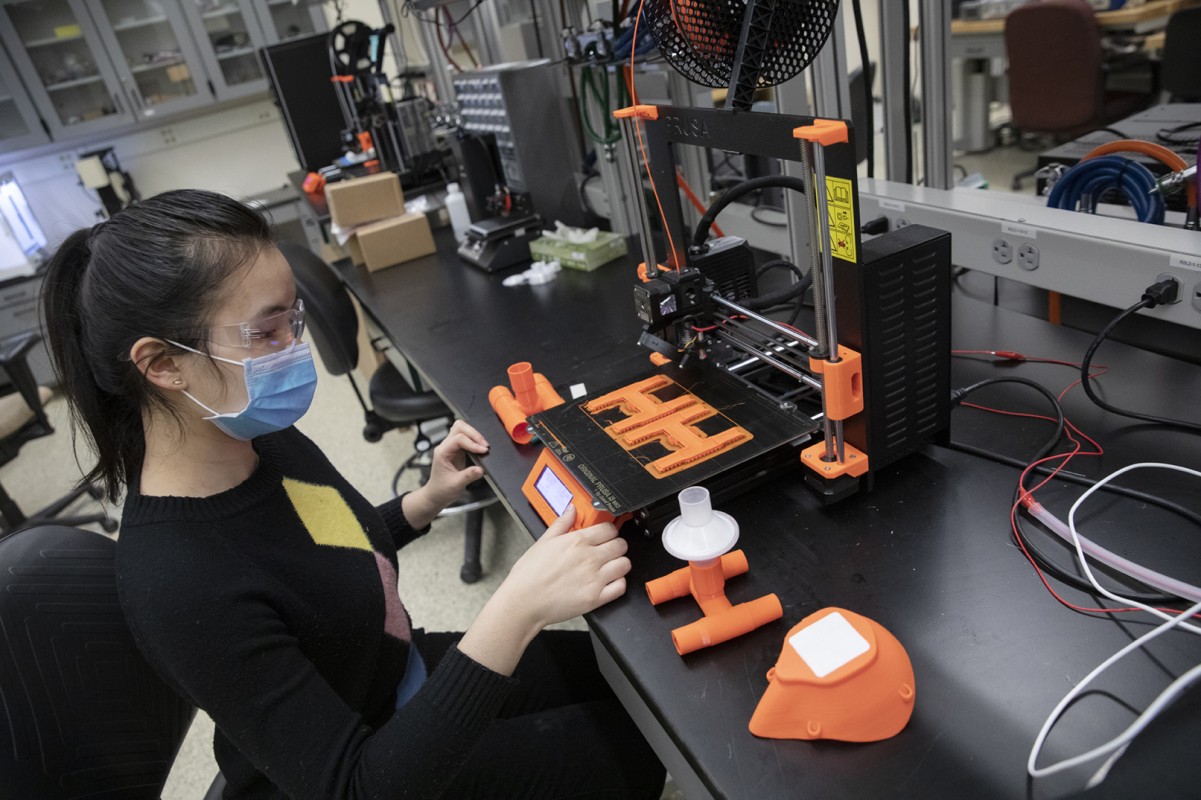
[UPDATED: March 27]
A lot can happen in a week, especially in the middle of a pandemic.
Just last Thursday (March 19), as Binghamton University students and faculty moved all classes online due to warnings about spreading COVID-19, a team of professors, graduate students and staff from the Thomas J. Watson School of Engineering and Applied Science began to help regional healthcare providers with their fight against the virus.
“Binghamton University is offering important supplies and problem-solving skills to fight COVID-19 in our community,” said President Harvey Stenger. “We are ready to give whatever aid we can to reduce the effects of this virus among our friends and neighbors.”
Four projects have made significant headway, working in partnership with local healthcare providers Lourdes and UHS.
“I am proud that the Watson School faculty and staff are uniting to face these unprecedented challenges,” Watson School Dean Krishnaswami “Hari” Srihari said. “It is a pleasure and an honor to work with them.”
Ventilator adapters
Earlier this week, as coronavirus cases in New York surged, Gov. Andrew Cuomo said the state needs at least 30,000 ventilators to care for the influx of coronavirus patients that is expected to hit in early April. The shortage of breathing machines already has been deadly in Italy, China and other hard-hit regions.
One emergency option would be to connect multiple patients to one ventilator using an adapter. It’s not an ideal scenario, but it could work temporarily if there’s a large influx of people requiring critical care.
Fuda Ning and Jia Deng (both assistant professors in the Department of Systems Science and Industrial Engineering) have been working with Scott Schiffres (an assistant professor in the Department of Mechanical Engineering) and four graduate students (Hamzeh Shraida, Shantanu Gaurkhede, Dayue Jiang and Huimin Zhou) to design and 3D-print these ventilator adapters. As each prototype has been printed, medical professionals at UHS and Lourdes are testing them and offering suggestions.
“At the very beginning, when we checked YouTube videos about these adapters, they only had the idea — they did not have the design,” Deng said. “We’ve had to spend a lot of time to design, to refine the design, to modify it and to test it.”
The adapters are made from PETG, a glycol-modified version of polyethylene terephthalate known for its chemical resistance, durability and formability. The Watson team has tried a variety of designs, allowing two to six patients to use one ventilator, but a four-patient design seems to be the most promising.
Binghamton University can print the few dozen adapters potentially needed for Greater Binghamton hospitals, and their 3D designs are online (thanks in part to Mo Sha from the Department of Computer Science) so that they can be printed anywhere that might need them.
“If those designs go well or can be certified by healthcare workers, it will be beneficial statewide, nationwide or even worldwide,” Deng said.
N95 masks
Ning and Deng also are working alongside professors from Watson’s Department of Biomedical Engineering to improve an internet-sourced design for reusable N95-style face masks.
The masks utilize two different types of plastic: The softer polydimethylsiloxane (PDMS) to create a tight seal around the nose and mouth, and the more rigid PETG to hold high-efficiency particulate air (HEPA) filters over the breathing hole. The Watson team obtained the electrostatically charged filters at a local home-improvement store and are cutting them down for size.
One of the challenges with this project, Ning said, has been bonding the two plastics into a cohesive unit.
“We need to generate a good seal,” he said. “It needs to conform correctly to the faces. We also need to think about the filter, to make sure that the function will be similar to the N95 masks. Then we can change the filter and reuse the mask.”
Professor Mohammad Khasawneh, chair of the SSIE department, is thrilled at the progress that the Watson School has made in a short time: “They’ve been working truly around the clock. It’s been amazing. They are passionate, dedicated and genuinely want to help.”
Zhou, an SSIE PhD student, has helped to design and print the ventilator adapters and face masks. Each adapter takes about 15 hours to make using Watson’s 3D printers, and about 10 hours is required for a mask. Like her colleagues, she’s been working long hours but knows why her efforts are important.
“Every day, I pass UHS and see that there are some tents up in the parking lot to prepare for extra patients who could need medical care,” she said. “I can see that our work will help people, and that makes me proud.”
UV sterilizing
Over the weekend, Srihari and Professor Kaiming Ye (chair of the BME department) delivered several thousand disposable gloves, 600 surgical masks, 29 N95 masks and several disposable gowns from Watson School supplies to UHS hospitals as a donation.
With supplies at hospitals running low for the foreseeable future, however, another design avenue for the Watson team is a way to sterilize standard-issue N95 masks using ultraviolet light so that they could be used more than once. The method also could be used on gowns, face shields and equipment contaminated by COVID-19.
“We don’t have any data about COVID-19, but we found a study about the efficiency of UV light to kill viruses,” Ye said. “We looked at the data on SARS and other coronaviruses — not this one, but very similar ones. We put this data into the computational model that we established to calculate the dosage needed to kill the virus on a surface and in the filter layer that is a major component of the N95 masks.”
With design help from BME faculty Fake “Frank” Liu, Guy German and Ying Wang, the sterilization stations feature large UV bulbs and foil to increase the amount of energy available to kill COVID-19 on any surface. Staff members at Watson School’s new Fabrication Lab built the stations for delivery to UHS and Lourdes.
“Right now, we can’t have in-person meetings, but scientists are adaptable in that way,” Ye said. “We can meet in virtual space, sketch the design, discuss the science and the data, argue about the calculations, and then everyone contributes to the solutions.”
Face shields
During some medical emergencies, healthcare workers require the extra protection that full-face shields offer, and those shields also are in short supply at many hospitals.
Leading an effort to design easily manufactured shields is Vince Brady, the Watson School’s manager of engineering laboratories and learning environments. Contributing to the prototype — which was built in the Fab Lab — were Schiffres, Deng, Benson Chan (associate director of the Integrated Electronics Engineering Center), Mark Poliks (director of the Center for Center for Advanced Microelectronics Manufacturing) and others.
Lourdes provided a sample face shield, Brady said, and the Watson team ran with the idea: “We took the basic concept, put it into the CAD [computer-aided design software] and created the program to cut these out using our new water jet. That was successful. It’s a basic three-piece assembly: Cut out the face shield, attach the foam headband, add the elastic and we’re done.”
With assistance from an industry partner, a few thousand shields could be produced quickly.
“They would have the ability to scale up and do the assembly work,” Brady said. “The initial feedback is good, so we’re just waiting to hear more.”
He is particularly grateful that renovations to the Fab Lab — part of a $22 million upgrade to the Engineering Building — were nearly completed by the time that COVID-19 arrived in the U.S. from other countries: “The timing really couldn’t have been any better. It’s really nice. We wouldn’t have been able to do the development and quick response that we’ve been doing.”