Research looks to improve ’green’ steel process using hydrogen instead of carbon
Professor receives $470,700 grant from National Science Foundation to study oxide reduction on atomic level
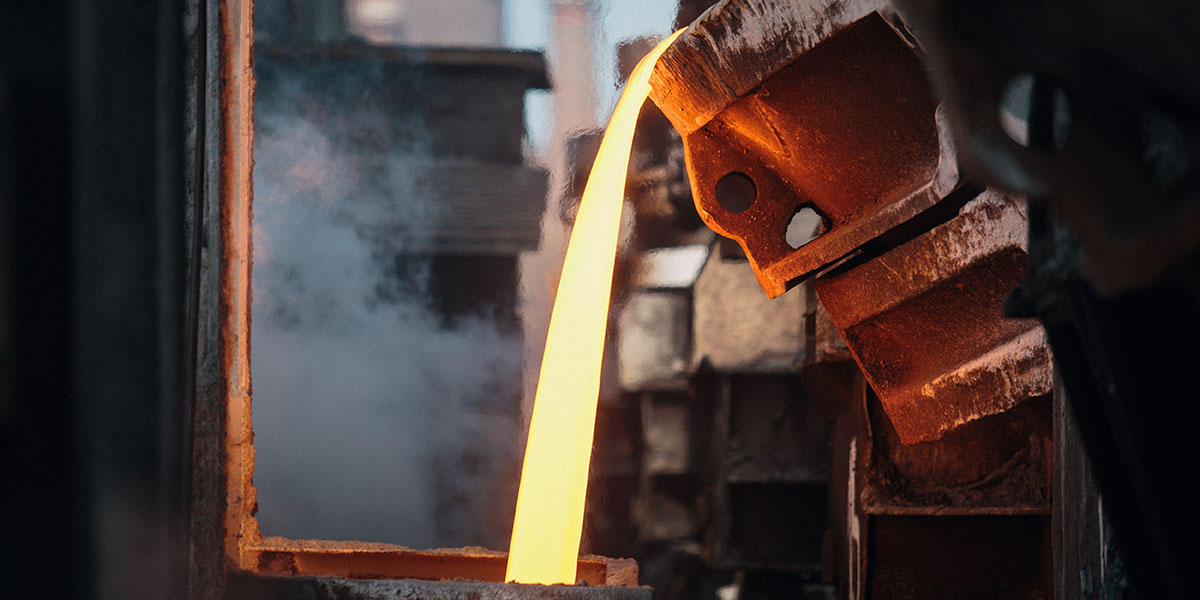
Steel is one of the most important industrial materials, with more than 2 billion tons produced annually around the world. Because of its high tensile strength and low cost, steel is used in everything from building construction and electrical appliances to ships, trains, cars and bicycles.
The steelmaking process, however, comes at a steep price for the environment, accounting for 7 to 11% of all human-made greenhouse gas emissions. If the steel industry were its own separate country, it would rank as the fifth-largest producer of carbon dioxide.
Traditionally, smelters make steel by removing oxygen from iron ore through a carbothermic approach that mixes iron oxide with carbon and intense heat. Facing escalating pressure from governments and investors to reduce emissions, the steel industry is experimenting with green steel projects that use hydrogen instead of carbon-intensive manufacturing.
Exactly how hydrogen-based direct reduction works, however, is not fully understood. Binghamton University Professor Guangwen Zhou, a faculty member in the Thomas J. Watson College of Engineering and Applied Science’s Department of Mechanical Engineering, recently received a $470,700 grant from the National Science Foundation to research the process on an atomic level.
“If you look at the reduction of iron oxides with hydrogen, it looks quite simple,” Zhou said. “You produce iron and water. In reality, it’s actually quite complicated because the reaction involves several other intermediate solid phases. We need to look at which path can be further improved to get better efficiency.”
As associate director of Binghamton’s Institute of Materials Research and deputy director of the materials science and engineering program, Zhou has been studying metal oxides for more than a decade. In 2011, his research earned him an NSF CAREER Award, which supports early-career faculty who have the potential to serve as academic role models in research and education.
More recently, he teamed up with the Brookhaven National Laboratory and other collaborators for two major studies of oxide reactions in real time, offering new insights into how the process works and how to control the reactions.
For this new NSF grant, Zhou is the principal investigator, but he and his students will use Brookhaven’s equipment, including environmental transmission electron microscopy (TEM) and ambient-pressure X-ray photoelectron spectroscopy (AP-XPS) to study possible pathways to reduce iron from iron oxide at temperatures exceeding 1,000 degrees Celsius (1,800 degrees Fahrenheit).
“We want to provide a fundamental understanding on the basic chronology of the reaction process and its complicated transformations,” he said. “Once we know that, we can play with factors like the amount of hydrogen, the pressure or the temperature to optimize the process.”
As the planet sweats through the hottest summer on record, cutting carbon emissions seems more urgent than ever.
“I think this project comes at the right time,” Zhou said. “There’s a lot of interest from the research community and from society, because of the need to reduce greenhouse gases.”